EDI pollution judgment and solution full version analysis
2021-03-09
one
Judgment of EDI membrane block fouling
one
Chemical cleaning and regeneration of equipment
Although the influent conditions of EDI membrane block greatly reduce the chance of blocking inside the membrane block, with the extension of equipment operation time, the channel inside EDI membrane block may still be blocked. This is mainly because there is more solute in EDI influent, which forms salt precipitation in the concentrated water chamber. If the influent contains a lot of calcium and magnesium ions (hardness more than 0.8ppm), CO2 and higher pH value, the precipitation rate will be accelerated. In this case, we can use chemical cleaning method to clean the EDI film block to restore its original technical characteristics.
two
Judgment of EDI membrane block being polluted and blocked
1. Under the condition of constant inlet temperature and flow rate, the pressure difference between the inlet side and the production side is 45% higher than the original data.
2. Under the condition of constant inlet temperature and flow rate, the pressure difference between concentrated water inlet side and concentrated water discharge side increases by 45% compared with the original data.
3. Under the condition of constant inlet temperature, flow rate and conductivity, the water quality (resistivity) decreased significantly.
4. Under the condition of constant inlet water temperature and flow rate, the concentrated water drainage flow decreased by 35%.
three
Several forms of membrane block blockage
1. Particle / colloid fouling
2. Inorganic pollution and blockage
3. Organic pollution and blockage
4. Microbial fouling
EDI cleaning note: before cleaning or disinfection, please select appropriate chemicals and be familiar with safe operation procedures. Do not carry out chemical cleaning without cutting off the power supply of components.
Particle / colloid fouling
When the inlet particle size is more than or equal to 5 μ m, the inlet channel will be blocked, resulting in the uneven distribution of water flow in the membrane block, and the overall performance of the membrane block will be reduced. If the inlet water of EDI membrane block does not directly enter EDI membrane block from RO water producing end, but supplies water through RO water producing tank through booster pump, it is recommended to add security filter (≤ 0.2 μ m) in front of EDI membrane block. When assembling EDI equipment, all connecting piping systems shall be flushed to prevent particulate impurities from entering the membrane block.
Inorganic pollution
If the EDI inlet water contains more solutes and exceeds the design value or the recovery rate exceeds the design value, it will lead to scaling in the concentrated water chamber and cathode chamber, resulting in precipitation of salt substances. Generally, the type of scaling is carbonate formed by calcium and magnesium ions. Even if the concentration of this kind of substance is very small and the contact time is very short, with the accumulation of operation time, there is still the possibility of scaling, and the hardness scaling is easy to be removed by pickling. According to the method in scheme 1, the scaling in the concentrated water chamber and cathode chamber can be removed by circulating the low pH solution in the system.
When the iron and manganese content in the influent is high, or the water with high TDS enters into EDI membrane block, the ion exchange resin in the fresh water chamber or the concentrated water chamber will also form little pollution. Option 2 can be used for cleaning.
Organic pollution
When the TOC or tea content of the influent exceeds the design standard, the ion exchange resin and ion-exchange membrane in the fresh water chamber will be blocked. The method of scheme 3 can be used to clean the fresh water chamber and the concentrated water chamber with high pH solution. The organic molecules can be removed and the ion exchange resin can be used to clean the fouling.
Microbial fouling
When the operating environment of the equipment is suitable for the growth of microorganisms, or there are more bacteria and algae in the influent, the EDI membrane block and system will also have microbial fouling. The method in scheme 3 and 4 can be used for cleaning with high pH brine. If microbial fouling is serious, scheme 5 can be used for cleaning. If there is inorganic pollution at the same time, the pickling step can be added according to scheme 6.
For very serious microbial fouling, scheme 7 or 8 can be used to clean with high pH agent.
two
Eight cleaning schemes for EDI film block
one
Cleaning scheme 1 - cleaning of scaling in concentrated water chamber
1. Record all data before cleaning.
2. Separate the connecting pipeline between EDI equipment and other equipment
3. Connect the cleaning device to make the cleaning pump enter EDI membrane block through the concentrated water pipeline, and then return to the cleaning water tank. Open the concentrated water inlet and outlet valves, and close EDI fresh water inlet valve and produced water valve.
4. The cleaning water tank is equipped with 2% hydrochloric acid cleaning solution.
5. Start the cleaning pump, adjust the concentrated water inlet valve, and cycle the cleaning at the specified flow rate (pickling step). (see attached table)
6. Stop the cleaning pump, empty the waste liquid from the cleaning tank, and separate the concentrated water drain valve to the trench.
7. Continuously inject clean water (RO produced water) into the cleaning water tank and start the cleaning pump for continuous cleaning (flushing step).
8. Open EDI inlet valve and product valve, and flush the two water chambers at the same time.
9. Test the water quality of the concentrated water outlet side until it is close to the conductivity of the inlet side.
10. Each valve, restore the original design flow data.
11. Restore the connection between EDI pipes and other systems.
12. Turn on the power supply of PLC control cabinet, send power to EDI membrane block, turn it into normal operation, and record the data of initial operation.
two
Cleaning scheme 2 - fresh water room scaling cleaning
1. Record all data before cleaning.
2. Separate the connecting pipeline between EDI equipment and other equipment
3. Connect the cleaning device to make the cleaning pump enter the fresh water chamber and the concentrated water chamber of EDI membrane block respectively through the water inlet pipeline, and then return to the cleaning water tank to open all the inlet and outlet valves.
4. The cleaning water tank is equipped with 2% hydrochloric acid cleaning solution.
5. Start the cleaning pump, adjust the concentrated water and inlet valve respectively, and cycle the cleaning with the specified flow (pickling step). (see attached table)
6. Stop the cleaning pump, empty the waste liquid from the cleaning tank, and separate the concentrated water drain valve to the trench.
7. Continuously inject clean water (RO produced water) into the cleaning water tank and start the cleaning pump for continuous cleaning (flushing step).
8. Test the water quality of fresh water and concentrated water outlet side respectively until the conductivity is close to that of inlet side.
9. Adjust each valve and restore the original design flow data.
10. Shut down and restore the connection between EDI pipelines and other systems.
11. Turn on the power supply of PLC control cabinet, send power to EDI membrane block, and carry out regeneration (regeneration step) until the resistivity meets the effluent requirements.
12. Turn into normal operation and record the data of the first operation.
three
Cleaning scheme 3 - cleaning of organic pollutants
1. Record all data before cleaning.
2. Separate the connecting pipeline between EDI equipment and other equipment
3. Connect the cleaning device to make the cleaning pump enter the fresh water chamber and the concentrated water chamber of EDI membrane block respectively through the water inlet pipeline, and then return to the cleaning water tank to open all the inlet and outlet valves.
4. The cleaning solution of 1% sodium hydroxide (NaOH) + 2% salt (NaCl) is configured in the cleaning water tank.
5. Start the cleaning pump, adjust the concentrated water and inlet valve respectively, and cycle the cleaning with the specified flow rate (alkali cleaning step). (see attached table)
6. Stop the cleaning pump, empty the waste liquid from the cleaning tank, and separate the concentrated water drain valve to the trench.
7. Continuously inject clean water (RO produced water) into the cleaning water tank and start the cleaning pump for continuous cleaning (flushing step).
8. The water quality at the outlet side of the produced water and concentrated water was detected until the conductivity was close to that at the inlet side.
9. Adjust each valve and restore the original design flow data.
10. Shut down and restore the connection between EDI pipelines and other systems.
11. Turn on the power supply of PLC control cabinet, send power to EDI membrane block, and carry out regeneration (regeneration step) until the resistivity meets the effluent requirements.
12. Turn into normal operation and record the data of the first operation.
four
Cleaning scheme 4 - organic fouling and scaling
1. Record all data before cleaning.
2. Separate the connecting pipeline between EDI equipment and other equipment
3. Connect the cleaning device to make the cleaning pump enter the fresh water chamber and the concentrated water chamber of EDI membrane block respectively through the water inlet pipeline, and then return to the cleaning water tank to open all the inlet and outlet valves.
4. The cleaning water tank is equipped with 2% hydrochloric acid cleaning solution.
5. Start the cleaning pump, adjust the concentrated water and inlet valve respectively, and cycle the cleaning with the specified flow (pickling step). (see attached table)
6. Stop the cleaning pump, empty the waste liquid from the cleaning tank, and separate the concentrated water drain valve to the trench.
7. Continuously inject clean water (RO produced water) into the cleaning water tank and start the cleaning pump for continuous cleaning (flushing step).
8. The water quality at the outlet side of the produced water and concentrated water was detected until the conductivity was close to that at the inlet side.
9. The cleaning solution of 1% sodium hydroxide (NaOH) + 2% salt (NaCl) is configured in the cleaning water tank.
10. Start the cleaning pump, adjust the concentrated water and inlet valve respectively, and cycle the cleaning with the specified flow rate (alkali cleaning step). (see attached table)
11. Stop the cleaning pump, empty the waste liquid from the cleaning tank, and separate the concentrated water drain valve to the trench.
12. Continuously inject clean water (RO produced water) into the cleaning water tank and start the cleaning pump for continuous cleaning (flushing step).
13. The water quality at the outlet side of the produced water and concentrated water was detected until the conductivity was close to that at the inlet side.
14. Adjust each valve and restore the original design flow data.
15. Shut down and restore the connection between EDI pipelines and other systems.
16. Turn on the power supply of PLC control cabinet, send power to EDI membrane block, and carry out regeneration (regeneration step) until the resistivity meets the effluent requirements.
17. Turn into normal operation and record the data of the first operation.
Scheme 3 can be used for microbial fouling
Scheme 4 can be used for microbial fouling and scaling
five
Cleaning scheme 5 - severe microbial fouling
1. Record all data before cleaning.
2. Separate the connecting pipeline between EDI equipment and other equipment
3. Connect the cleaning device, make the cleaning pump enter the fresh water room and concentrated water room of EDI membrane block through the water inlet pipe, then return to the cleaning water tank, and open all the inlet and outlet valves.
4. The cleaning water tank is equipped with 2% salt (NaCl) cleaning solution.
5. Start the cleaning pump, adjust the fresh water and concentrated water inlet valve, and cycle the cleaning with the specified flow (salt washing step). (see attached table)
6. Stop the cleaning pump, empty the waste liquid from the cleaning water tank, and separate the produced water and concentrated water drain valve to the trench.
7. Continuously inject clean water (RO produced water) into the cleaning water tank and start the cleaning pump for continuous cleaning (flushing step).
8. The water quality at the outlet side of the produced water and concentrated water was detected until the conductivity was close to that at the inlet side.
9. 0.04% concentration of peracetic acid (ch3coooh) + 0.2% hydrogen peroxide (H2O2) cleaning solution was prepared in the cleaning water tank.
10. Start the cleaning pump, adjust the fresh water and concentrated water inlet valves respectively, and cycle the cleaning with the specified flow (disinfection step). (see attached table)
11. Stop the cleaning pump, empty the waste liquid from the cleaning tank, and separate the concentrated water drain valve to the trench.
12. Continuously inject clean water (RO produced water) into the cleaning water tank and start the cleaning pump for continuous cleaning (flushing step).
13. The water quality at the outlet side of the produced water and concentrated water was detected until the conductivity was close to that at the inlet side.
14. The cleaning water tank is equipped with 2% salt (NaCl) cleaning solution.
15. Start the cleaning pump, adjust the fresh water and concentrated water inlet valve, and cycle the cleaning with the specified flow (salt washing step). (see attached table)
16. Stop the cleaning pump, empty the waste liquid from the cleaning water tank, and separate the produced water and concentrated water drain valve to the trench.
17. Continuously inject clean water (RO produced water) into the cleaning water tank and start the cleaning pump for continuous cleaning (flushing step).
18. The water quality at the outlet side of the produced water and concentrated water was detected until the conductivity was close to that at the inlet side.
19. Adjust each valve and restore the original design flow data.
20. Shut down and restore the connection between EDI pipelines and other systems.
21. Turn on the power supply of PLC control cabinet, send power to EDI film block, and carry out regeneration (regeneration step) until the resistivity meets the requirement of water outlet.
22. Turn into normal operation, and record the data of initial operation.
six
Cleaning plan 6 - severe microbial fouling and scaling
1. Record all data before cleaning.
2. Separate the connecting pipeline between EDI equipment and other equipment
3. Connect the cleaning device, make the cleaning pump enter the fresh water room and concentrated water room of EDI membrane block through the water inlet pipe, then return to the cleaning water tank, and open all the inlet and outlet valves.
4. The cleaning water tank is equipped with 2% hydrochloric acid cleaning solution.
5. Start the cleaning pump, adjust the concentrated water and inlet valve respectively, and cycle the cleaning with the specified flow (pickling step). (see attached table)
6. Stop the cleaning pump, empty the waste liquid from the cleaning tank, and separate the concentrated water drain valve to the trench.
7. Continuously inject clean water (RO produced water) into the cleaning water tank and start the cleaning pump for continuous cleaning (flushing step).
8. Test the water quality of fresh water and concentrated water outlet side respectively until the conductivity is close to that of inlet side.
9. The cleaning water tank is equipped with 2% salt (NaCl) cleaning solution.
10. Start the cleaning pump, adjust the fresh water and concentrated water inlet valve, and cycle the cleaning with the specified flow (salt washing step). (see attached table)
11. Stop the cleaning pump, empty the waste liquid from the cleaning water tank, and separate the produced water and concentrated water drain valve to the trench.
12. Continuously inject clean water (RO produced water) into the cleaning water tank and start the cleaning pump for continuous cleaning (flushing step).
13. The water quality at the outlet side of the produced water and concentrated water was detected until the conductivity was close to that at the inlet side.
14. 0.04% concentration of peracetic acid (ch3coooh) + 0.2% hydrogen peroxide (H2O2) cleaning solution was prepared in the cleaning water tank.
15. Start the cleaning pump, adjust the fresh water and concentrated water inlet valves respectively, and cycle the cleaning with the specified flow (disinfection step). (see attached table)
16. Stop the cleaning pump, empty the waste liquid from the cleaning tank, and separate the concentrated water drain valve to the trench.
17. Continuously inject clean water (RO produced water) into the cleaning water tank and start the cleaning pump for continuous cleaning (flushing step).
18. The water quality at the outlet side of the produced water and concentrated water was detected until the conductivity was close to that at the inlet side.
19. The cleaning water tank is equipped with 2% salt (NaCl) cleaning solution.
20. Start the cleaning pump, adjust the fresh water and concentrated water inlet valve, and cycle the cleaning with the specified flow (salt washing step). (see attached table)
21. Stop the cleaning pump, empty the cleaning waste liquid from the cleaning water tank, and separate the produced water and concentrated water drain valve to the trench.
22. Continuously inject clean water (RO produced water) into the cleaning water tank and start the cleaning pump for continuous cleaning (flushing step).
23. Test the water quality of the outlet side of the produced water and concentrated water respectively until the conductivity is close to that of the inlet side.
24. Adjust each valve to restore the original design flow data.
25. Stop the machine and restore the connection between EDI pipelines and other systems.
26. Turn on the power supply of PLC control cabinet, send power to EDI membrane block, and carry out regeneration (regeneration step) until the resistivity meets the effluent requirements.
27. Turn into normal operation and record the data of initial operation.
seven
Cleaning plan 7 - severe microbial fouling
1. Record all data before cleaning.
2. Separate the connecting pipeline between EDI equipment and other equipment
3. Connect the cleaning device, make the cleaning pump enter the fresh water room and concentrated water room of EDI membrane block through the water inlet pipe, then return to the cleaning water tank, and open all the inlet and outlet valves.
4. The cleaning water tank is equipped with 2% salt (NaCl) cleaning solution.
5. Start the cleaning pump, adjust the fresh water and concentrated water inlet valve, and cycle the cleaning with the specified flow (salt washing step). (see attached table)
6. Stop the cleaning pump, empty the waste liquid from the cleaning water tank, and separate the produced water and concentrated water drain valve to the trench.
7. Continuously inject clean water (RO) into the cleaning water tank
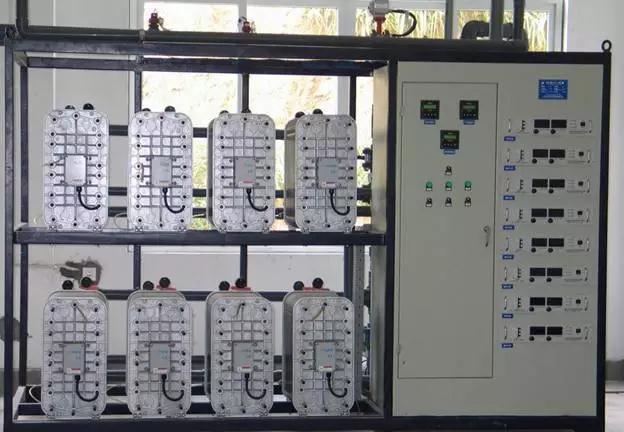